Experts in Foundry
Tooling & Design
Specialists in Foundry Tooling from Design, Simulation, Pattern Building, Molds, and Core Boxes.
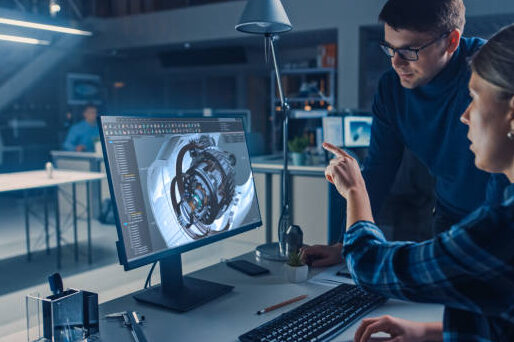
Engineering & Design Services
Our Engineering and design are tailored for your specific needs, offering customized solutions that precisely align with diverse foundry requirements. Our expert team collaborates closely with clients to translate unique specifications into meticulously crafted designs, ensuring optimal performance and efficiency for specialized applications.
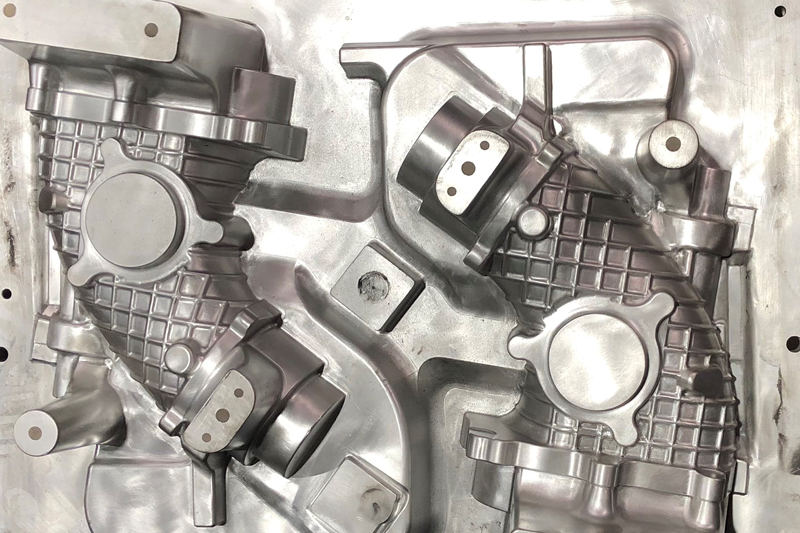
Patterns and Molds
Our pattern and mold production stands as a testament to precision and innovation. From intricate designs to customized solutions, we craft patterns and molds with a commitment to excellence, ensuring our clients receive top-tier products that elevate their foundry operations.
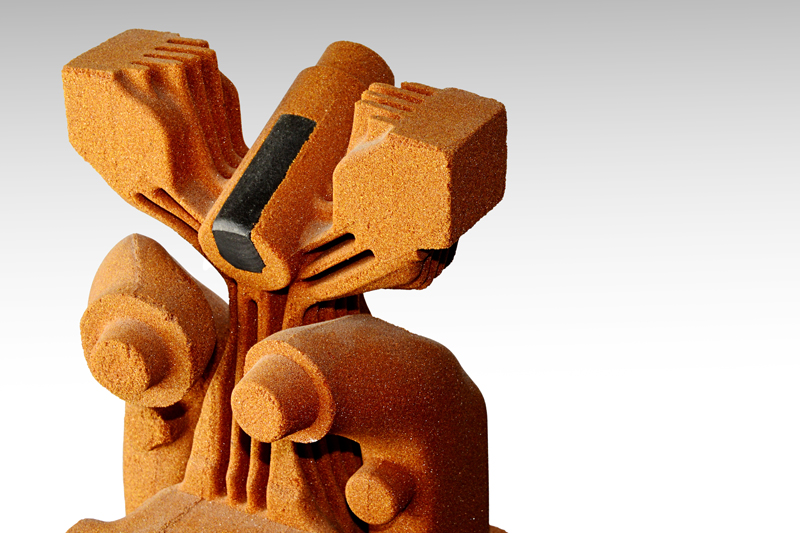
Core Boxes
Our core box production is characterized by a fusion of cutting-edge technology and meticulous craftsmanship. We specialize in creating versatile core boxes that cater to a spectrum of foundry applications, from conventional to highly specialized requirements. With a commitment to quality and innovation, our core box production exemplifies our dedication to providing tailored solutions that elevate the efficiency and precision of the casting process.
Want To Learn More? See All Our Services!
CUSTOM ENGINEERING & DEVELOPMENT OF EMERGENCY RESOURCING OF ENGINE COOLING COMPONENTS
HITECH Shapes and Designs, a division of Seilkop Industries, Inc., offers high production to prototype and foundry tooling and fabrication services. In-house prototyping capabilities extend beyond simple SLA printing to offer a more realistic representation of the production casting, including the required draft. Designers and engineers are experienced in all modern modeling CAD systems including Pro-E and SolidWorks to accommodate the customers’ design work into our system. QuickCAST is our proprietary simulation software that can model the entire casting process and pinpoint any expected issues in the part or tooling prior to manufacturing. This extensive prototyping and analysis saves time and money during the tooling fabrication and preproduction verification phases.
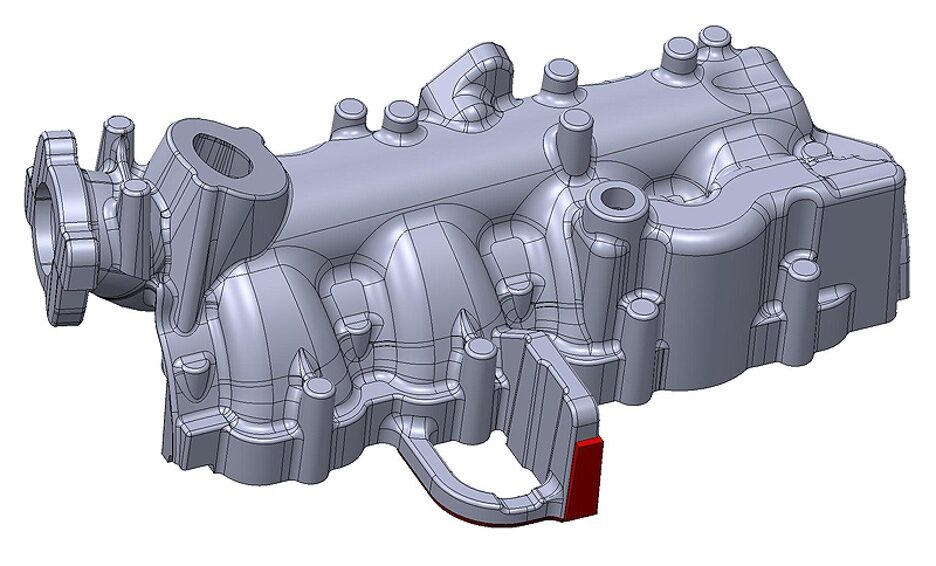
The tooling was subjected to full dimensional and functionality testing to ensure quality and integrity. The produced thermostat housing component as specified by the customer supplied 2D/3D CAD drawings. Turnaround time for this project was 3 weeks, shipped to the customer in Cincinnati, OH. For more details about this housing component pattern design and fabrication, or the full menu of services and capabilities available please see the table below or contact us directly.
Project Showcase
Our Associations
Let's Discuss Your Project
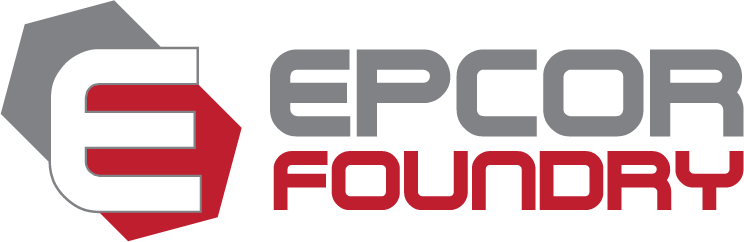
ALUMINUM SAND
CASTING & RAPID
PROTOTYPE CASTING
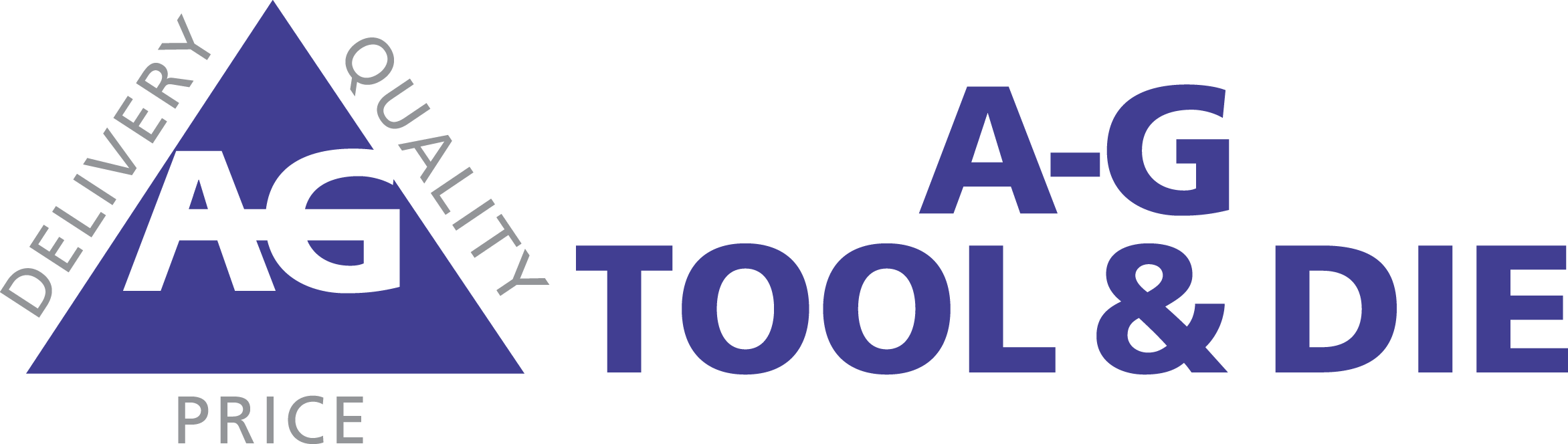
PROGRESSIVE & TRANSFER DIE MAKING, PRODUCTION READY TOOLING, & IN-HOUSE DESIGN & ENGINEERING SERVICES

OXY FUEL CUTTING AND BLANCHARD GRINDING, LARGE ROLL AND JOURNAL REPAIR, AND PRECISION DIE SETS
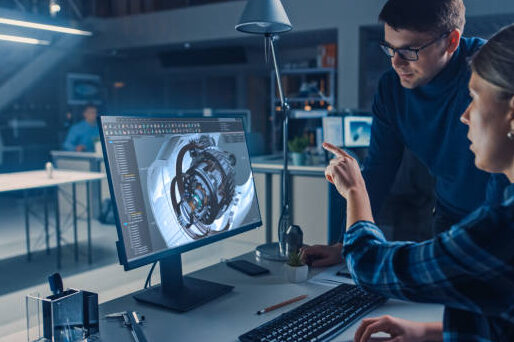