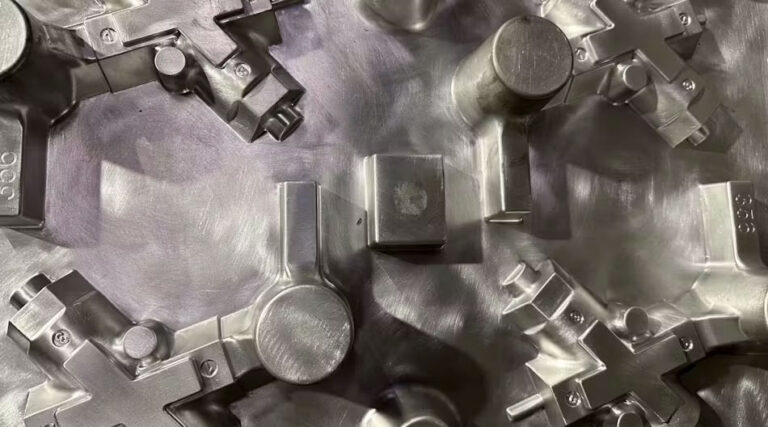
Why World-Class Tooling Drives Success
Foundries that make the right investments can catalyze improvements in profitability, production reliability, workforce satisfaction, and process customization.
The metalcasting market is highly competitive, and operational efficiency and quality are prerequisites for foundries’ sustainable growth. Many decades of experience by one foundry tooling manufacturer has shown that the right tooling investments can catalyze profound improvements in profitability, production reliability, workforce satisfaction, and process customization. By taking a strategic approach to upgrading tooling, foundries can reduce scrap costs, increase machine uptime, foster a motivated workforce, and implement solutions tailored to specific operating challenges.