Case Studies
CUSTOM ENGINEERING & DEVELOPMENT OF EMERGENCY RESOURCING OF ENGINE COOLING COMPONENTS
HITECH Shapes and Designs, a division of Seilkop Industries, Inc., offers high production to prototype and foundry tooling and fabrication services. In-house prototyping capabilities extend beyond simple SLA printing to offer a more realistic representation of the production casting, including the required draft. Designers and engineers are experienced in all modern modeling CAD systems including Pro-E and SolidWorks to accommodate the customers’ design work into our system. QuickCAST is our proprietary simulation software that can model the entire casting process and pinpoint any expected issues in the part or tooling prior to manufacturing. This extensive prototyping and analysis saves time and money during the tooling fabrication and preproduction verification phases.
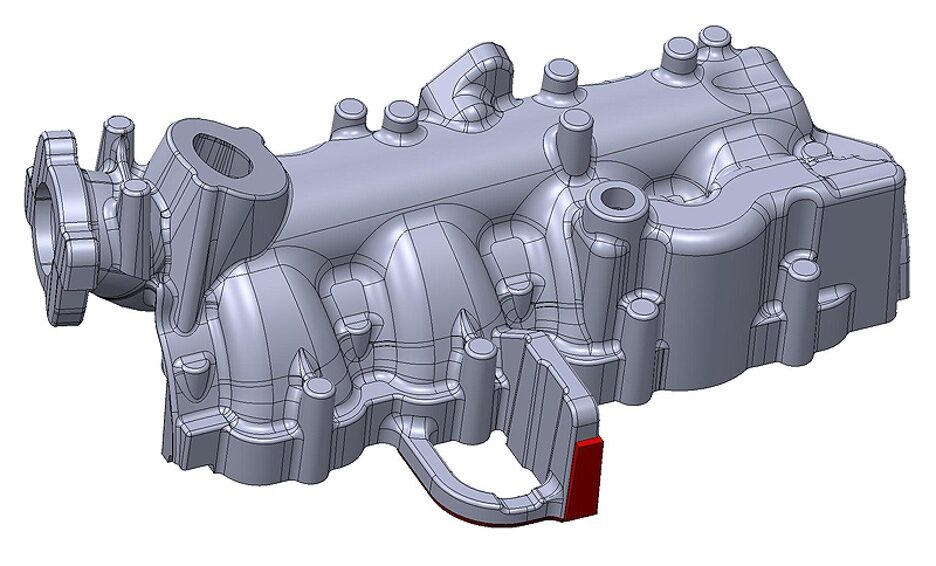
The tooling was subjected to full dimensional and functionality testing to ensure quality and integrity. The produced thermostat housing component, as specified by the customer supplied 2D/3D CAD drawings. Turnaround time for this project was 3 weeks, shipped to the customer in Cincinnati, OH. For more details about this housing component pattern design and fabrication, or the full menu of services and capabilities available please see the table below or contact us directly.
MANUFACTURING OF HIGH PRODUCTION STEEL SHELL MOLD PATTERNS
HITECH Shapes and Designs, a division of Seilkop Industries, Inc., was contracted by an Industry leader of compressor components, who required high speed milling of patterns to reduce draft required in casting process. The utilization of Hitech high speed milling and machining software was critical factor in the success of this project.
Our engineers developed the process and custom tooling, complete with 2D and 3D renderings and simulations. We were able to complete the machining of the tooling’s deep pockets while holding very tight tolerances of ±0.0005” with our advanced vertical milling machinery. The tooling was constructed with 4140 steel.
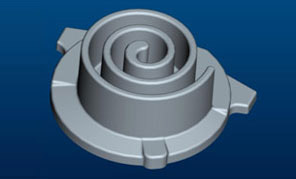
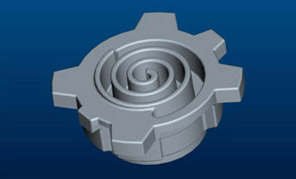
The completed pattern featured a micro machined finish of 3.2 micron, and a 1 micron hand polished finish, this rendered secondary finishing unnecessary. Comprehensive dimensional testing and functionality testing were carried out to ensure customer specifications for quality and integrity were met. The shell mold pattern was completed within a 3 week lead time, delivered to the customer in Eastern Ohio. For more details about this draft reducing custom shell mold pattern fabrication, or our precision manufacturing solutions please see the table below or contact us directly.
MANUFACTURING OF HIGH VOLUME PATTERN & CORE BOXES
HITECH Shapes and Designs, a division of Seilkop Industries, Inc., was contracted to handle an emergency situation for a customer in the automotive industry. Due to the inferior quality and unreliable delivery schedule of their current Asian supplier the company was facing an impending shut down of an engine line, and needed a high performing solution on an accelerated timeline. With mere weeks to build the tooling, we developed a temporary tooling solution for immediate part production, simultaneously fabricating the production tooling to meet the ongoing high volume production requirements of the part. Employing advanced vertical milling machinery, the pattern was precision machined from D2 and steel. The tightest tolerances of ±0.0005” were held.
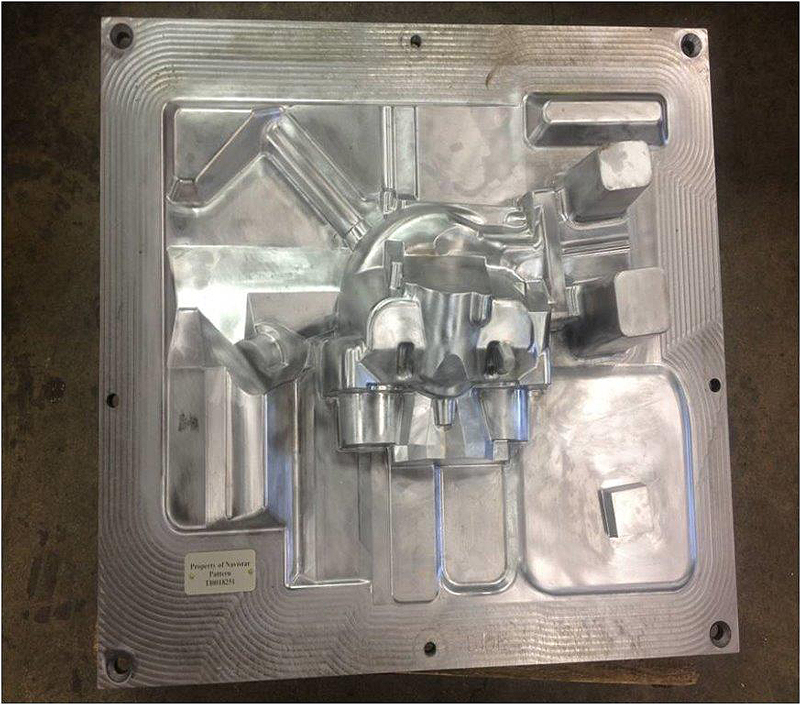
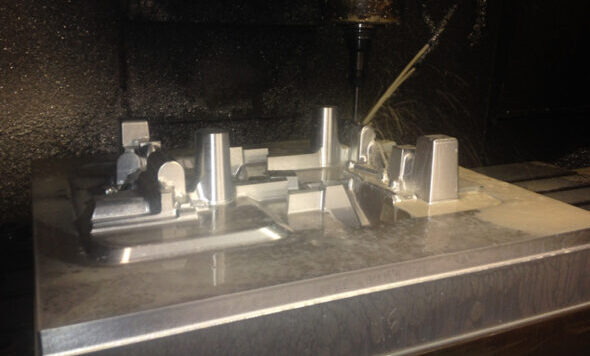
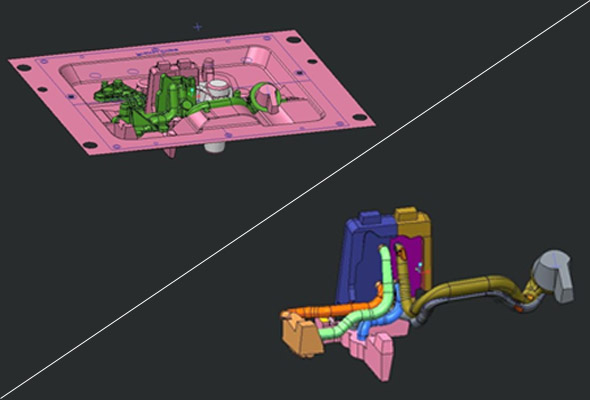
Our Associations
Let's Discuss Your Project
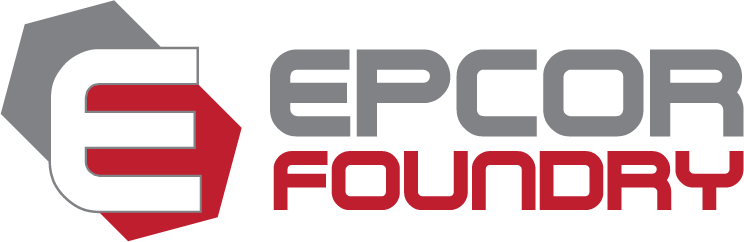
ALUMINUM SAND
CASTING & RAPID
PROTOTYPE CASTING
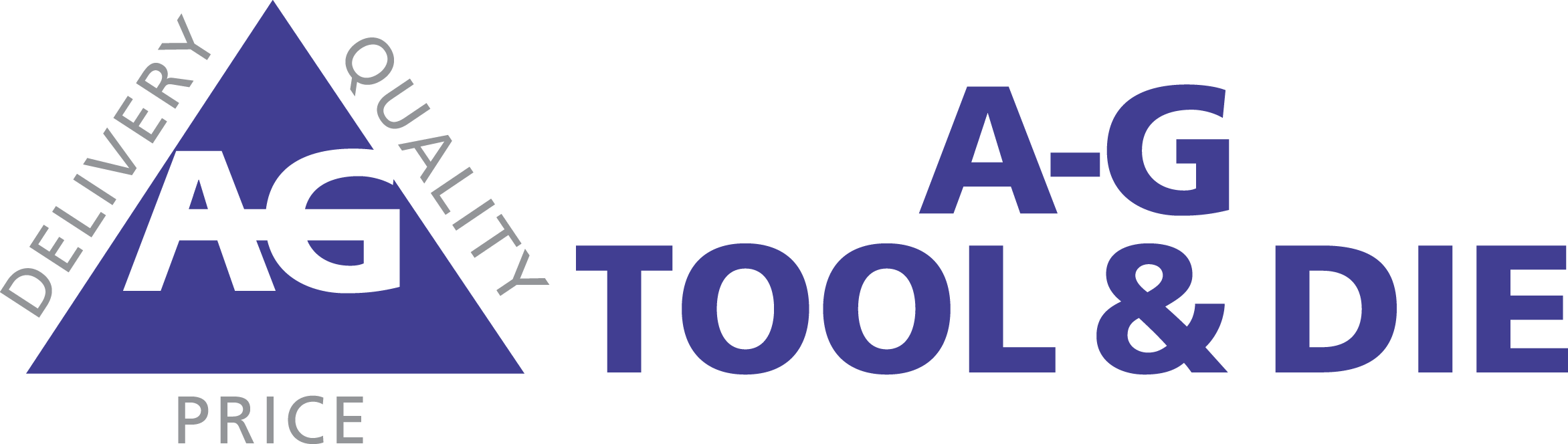
PROGRESSIVE & TRANSFER DIE MAKING, PRODUCTION READY TOOLING, & IN-HOUSE DESIGN & ENGINEERING SERVICES

FOUNDRY, TOOLING, THEDESIGN SIMULATION &BUILDING OF PATTERNS, MOLDS, CORE BOXES & MORE
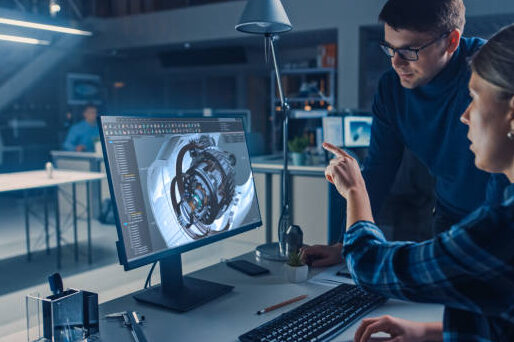