A Quality Manufacturing Process Makes Quality Castings
HITECH Shapes and Designs, a division of Seilkop Industries, Inc., offers high production to prototype and foundry tooling and fabrication services. In-house prototyping capabilities extend beyond simple SLA printing to offer a more realistic representation of the production casting, including the required draft. Designers and engineers are experienced in all modern modeling CAD systems including PowerShapes and SolidWorks to accommodate the customers’ design work into our system. QuickCAST is our proprietary simulation software that can model the entire casting process and pinpoint any expected issues in the part or tooling prior to manufacturing. This extensive prototyping and analysis saves time and money during the tooling fabrication and preproduction verification phases.
We have a full in-house pattern shop capable of designing and fabricating patterns and cores for virtually all casting systems including vertical and horizontal DISA, Sinto, and Hunter patterns. Patterns can be fabricated for sand casting, permanent mold, or shell mold applications. Core equipment includes Redford, Harrison, Laempe, and Hottinger core machines for both hot and cold core box manufacturing. All tooling is CNC machined to precision tolerances from cast iron, steel, aluminum, urethane, hardwood, or plastic. Turning centers are equipped with live tooling and capable of turning material up to 12” in diameter. Milling centers have a cutting diameter of 20” and can machine parts up to 54” x 30” x 26”. We are an ISO 9001:2015 certified company and have been an industry leader in the production of foundry tooling since 1946. Our customers include the automotive, compressor, marine, and pump component industries.
ISO 9001:2015 CERTIFIED
HITECH Shapes & Designs has met the requirements of ISO 9001:2015 for the manufacture of sand cast and permanent mold aluminum alloy castings and machined parts.
To view our ISO 9001:2015 certificate, please click the button below.
Project Showcase
Custom Engineering & Development of Emergency Resourcing of Engine Cooling Components
Let's Discuss Your Project
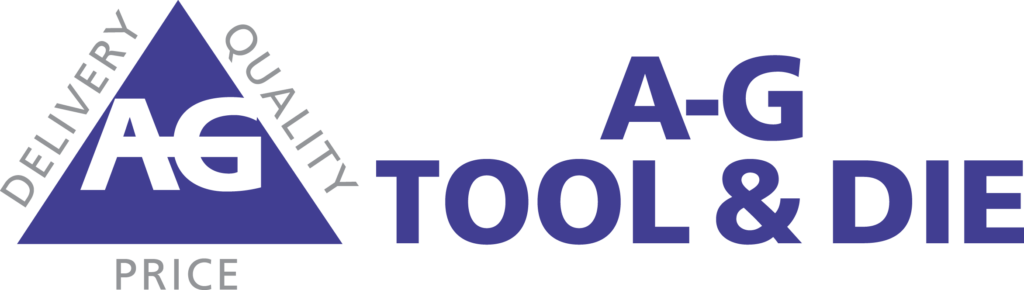
PROGRESSIVE & TRANSFER DIE MAKING, PRODUCTION READY TOOLING, & IN-HOUSE DESIGN & ENGINEERING SERVICES
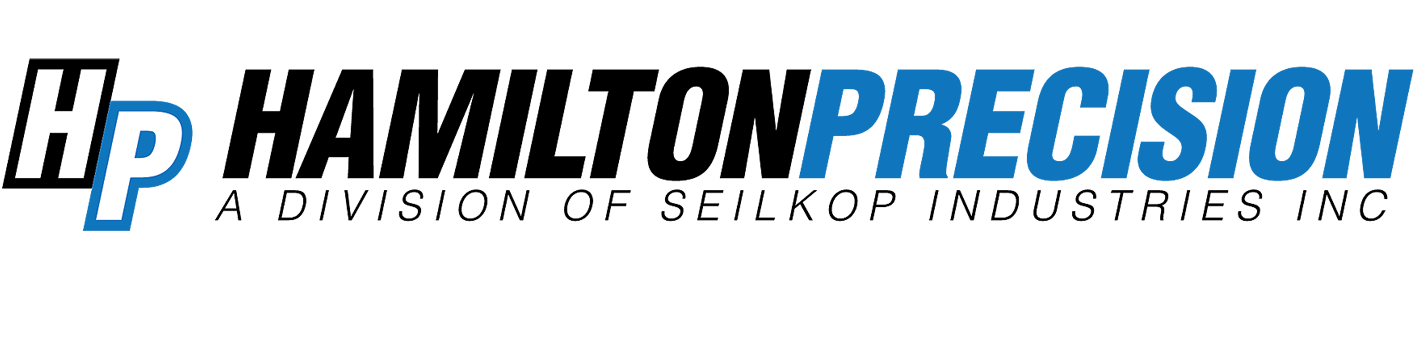
FOUNDRY, TOOLING, THEDESIGN SIMULATION &BUILDING OF PATTERNS, MOLDS, CORE BOXES & MORE
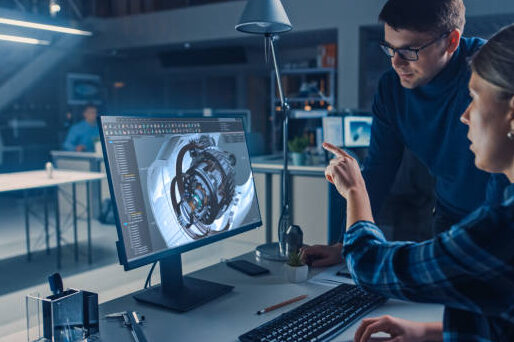
Keep up with the Latest HITECH Shapes & Designs News! Subscribe to Our Newsletter!
